Cyrus are not the only company to recognise the importance of the power supply. But they were one of the 1st.
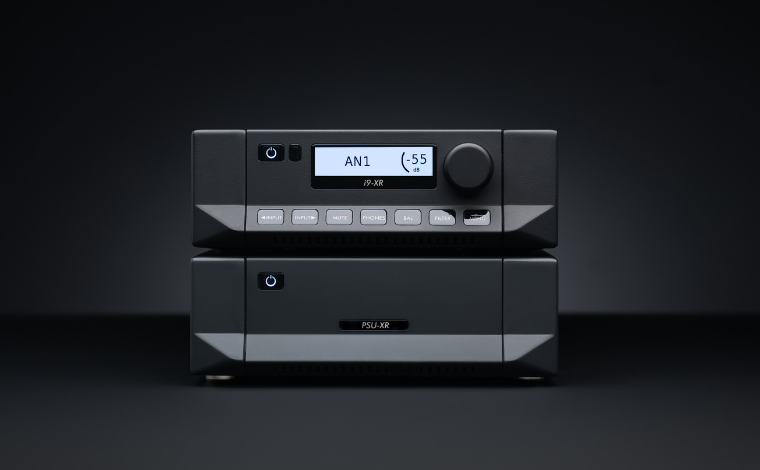
The sound quality delivered by any audio component, whether an amplifier or a source component such as a CD player, depends heavily upon the quality and capacity of its power supply. The PSU-XR power supply upgrade provides a sound upgrade for Cyrus XR components by enhancing both the quality and capacity of their internal power supplies.
Specification
- Low voltage supply - Standby mode +5V DC
- Low voltage supply - Operational +5V DC
- Fixed voltage supply - Standby mode 0V
- Fixed voltage supply - Operational +24V DC
- Variable supply - Standby mode 0V
- Variable supply - Regulated +10V to +45V DC
- Variable supply - Unregulated +45V or +56V DC
- Size (H x W x D) 75 x 215 x 355 mm (2.95” x 8.46” x 13.98”)
- Weight 7.7kg (17lbs)
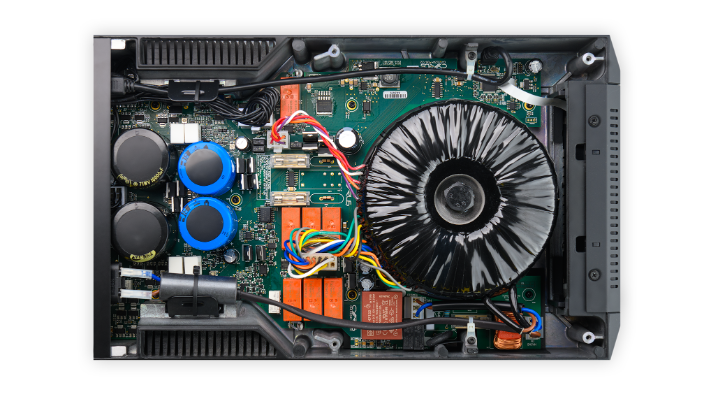
There are five independent power supplies in the PSU-XR. All five power outputs route to a connected XR component through a multi-way umbilical cable:
- A high capacity logic supply to power digital circuitry in a connected XR component.
- Two fixed voltage power supplies that are intended to power sensitive, low voltage analogue circuitry.
- Two variable voltage high capacity power supplies to feed power to low or high consumption analogue circuitry. The variable power supplies also have two unregulated voltage settings that can be applied to boost the power supply in high consumption circuitry such as power amplifiers.
Fifteen separate transformer windings, ground isolated regulation circuitry and separate output power and ground returns in the umbilical cable minimise electrical noise in the multiple power feeds to a connected XR component.
PSU-XR configuration takes place via the cable from the connected XR component. Each Cyrus design can enable and configure the power supplies in the PSU-XR to meet its circuit requirements exactly.
Hear it for yourself. Now in store and on demo.